Introduction
Root cause analysis (RCA) is a problem-solving methodology that aims to identify the underlying cause of an issue to prevent it from reoccurring. RCA has evolved in various industries, including healthcare, manufacturing, aviation, and engineering. In this article, we will discuss the basics, benefits, and steps of RCA. But why knowing RCA is essential? Let’s find out.
Root Cause Analysis 101: An Introduction to Solving Problems at their Source
RCA is a proactive approach that focuses on finding the real cause of a problem rather than dealing with its symptoms. It involves investigating the event or occurrence to identify the causal factors and underlying issues. RCA helps in identifying the “root cause,” which can be addressed through specific corrective actions. The primary benefit of RCA is that it helps organizations in preventing incidents and improving their process. RCA is often used in situations that require a significant investigation, such as accidents, product defects, critical incidents, and service failures.
The Importance of Root Cause Analysis in Preventing Future Issues
RCA is essential to prevent future issues as it helps eliminate the recurrence of a problem. By identifying the root cause of a problem, it is possible to address the issue, implement effective controls and reduce the likelihood of recurrence. The advantage of preventing future issues is that it saves time, improves efficiency, and enhances an organization’s reputation. For example, by identifying overuse of production machinery as a root cause of equipment malfunctions, a manufacturing plant can implement a preventive maintenance program for better equipment management, reducing downtime and overhead costs.
5 Steps to Conducting a Successful Root Cause Analysis
RCA typically involves five steps, which are as follows:
- Define the problem: This step involves defining the issue and understanding its impact.
- Gather data: In this step, the team collects and analyzes relevant data related to the problem.
- Identify possible causal factors: This step involves brainstorming to identify possible causes of the problem.
- Analyze data: In this step, the team evaluates the data and identifies the most likely root cause of the problem.
- Develop and implement corrective actions: Based on the analysis, the team formulates and implements corrective actions to prevent future issues.
The RCA process is iterative, which means that the steps can be repeated until the true root cause is identified, and effective corrective actions are implemented.
How to Use Root Cause Analysis to Improve Your Business Processes
RCA can improve business processes by helping in identifying and eliminating inefficiencies and process failures. For example, a company may conduct an RCA of the hiring process to identify the root cause of low retention rates. The analysis may reveal that the lack of a robust onboarding process is the root cause of the high turnover rate. The company can then implement a comprehensive onboarding process to eliminate the issue, ensuring employee retention. In summary, RCA can help businesses in identifying and addressing the root cause of process issues, improve efficiency, and reduce costs.
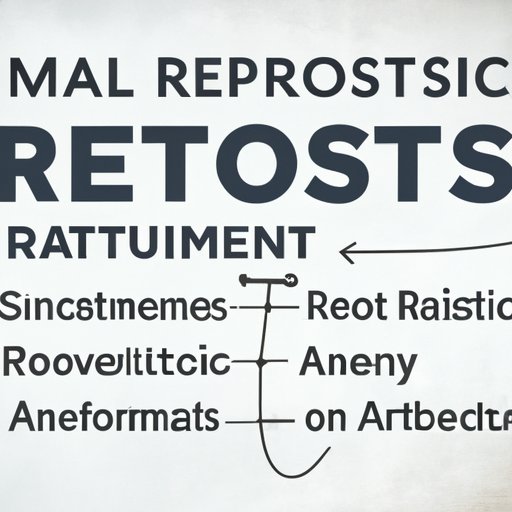
Real Life Examples of Effective Root Cause Analysis
Root cause analysis has been effective in identifying and addressing complex problems in various industries. For example, in aviation, RCA helped in identifying the cause of the crash of Air France Flight 447. After the accident, investigators used RCA to identify the root cause of the system malfunction, which led to the crash. As a result, the aviation industry took corrective measures to prevent similar accidents. Similarly, in the healthcare sector, RCA has been used extensively to improve patient safety by identifying and eliminating medical errors.
The Role of Root Cause Analysis in Safety Incident Investigations
RCA plays a crucial role in safety incident investigations in industrial settings. In safety incidents, such as accidents, injuries, or hazardous spills, RCA is used to identify the root cause of the event, including the system and human factors. By identifying the cause, it is possible to take corrective actions and prevent similar incidents in the future. For example, RCA can help in identifying the root cause of machine malfunctions that led to an industrial accident and implementing preventative maintenance programs to reduce the likelihood of future accidents.
Common Mistakes to Avoid When Conducting Root Cause Analysis
Root cause analysis can be challenging, and there are common mistakes that investigators may make. Some of the most common mistakes are inadequate data collection, failure to involve stakeholders, jumping to conclusions, and focusing on the symptoms rather than the root cause. To avoid these mistakes, it is essential to follow the RCA process systematically with the involvement of a cross-functional team, gather all relevant data, and use analytical tools and techniques when analyzing the data.
Conclusion
In conclusion, root cause analysis is an essential methodology that helps organizations in identifying and addressing underlying issues to prevent future issues. RCA involves specific steps, such as defining the problem, gathering relevant data, identifying possible causal factors, analyzing the data, and implementing corrective actions. By using RCA, businesses can improve their process efficiency, reduce costs, and enhance their reputation. However, it is essential to avoid common mistakes when conducting RCA to ensure the process’s effectiveness.