I. Introduction
When it comes to troubleshooting electrical systems, one common issue that occurs is a malfunctioning relay. A relay is a device that allows a low-power signal to control a higher-power circuit, making them a critical component in many electrical systems. Testing relays regularly is crucial to avoid any potential risks, including damage to equipment or personal injury.
II. Types of Relays and Their Uses
There are several types of relays, each with unique functions and purposes. Understanding the different types can help in determining the most appropriate method to use when testing.
A. Electromagnetic Relays
Electromagnetic relays operate by magnetizing a metal bar using an energized coil, which causes a mechanical lever to move and close or open a circuit. They can handle high currents and are often used in low voltage applications, such as switching on and off lights, motors, and other similar equipment.
B. Solid-State Relays
Solid-state relays are composed of semiconductors that provide a solid-state alternative instead of using electromagnetic coils. They are preferred for applications that require high-speed and quiet operation, with little or no sparking when the contacts switch position. Solid-state relays are typically used in computers, medical equipment, and other sensitive, high-precision components.
C. Time Delay Relays
Time delay relays allow for a delay in time between the activation and deactivation of circuits. They are employed in applications that require precise timing control, such as industrial controls, automated equipment, and traffic signals.
D. Thermal Overload Relays
Thermal overload relays contain thermal elements that measure temperature and can shut off equipment if they reach a specified limit. They are used in applications that require protection from overheating, such as motors and other electrical devices.
E. Contactors
Unlike the other types of relays, contactors are specifically designed to switch power to an electrical load, usually a motor. They usually require less current to operate and are often used in HVAC and industrial applications.
III. How to Test Each Type of Relay
A. Electromagnetic Relays
To test an electromagnetic relay, you should:
- Disconnect the relay coil from any source
- Test the continuity of the coil using a multimeter or an ohmmeter. The resistance should be within the specified range provided by the manufacturer.
- Test the contacts by using a multimeter or an ohmmeter to check for continuity.
B. Solid-State Relays
To test a solid-state relay, you should:
- Check the input circuit by using a multimeter to test the control voltage. The voltage should be within the range specified by the manufacturer.
- Check the output circuit by using a multimeter to test for continuity or resistance.
- Verify the switching time by using an oscilloscope to measure the time between the control signal and the switching action.
C. Time Delay Relays
To test a time delay relay, you should:
- Check the timing delay by using a multimeter or oscilloscope to verify the delay time specified by the manufacturer.
- Check the timing delay repeat accuracy by using a stopwatch and counting the number of times the relay switches on and off within a specified time frame.
- Check the drop-out time by using an oscilloscope to verify the time it takes between the removal of the input signal and the switching of the relay.
D. Thermal Overload Relays
To test a thermal overload relay, you should:
- Test the thermal relay mechanism by heating the relay with a heat gun or hair dryer and watching for switch-off at the specified temperature.
- Test the overload contacts by using a multimeter to check for continuity or resistance.
- Check the control circuitry by measuring the voltage supplied to the control coil with a multimeter. It should be within the manufacturer’s range.
E. Contactors
To test a contactor, you should:
- Test the contactor coil by checking the resistance using a multimeter. It should be within the range specified by the manufacturer.
- Test the contacts by using a multimeter to check for continuity or resistance.
- Check for damage and alignment by inspecting for signs of wear or misalignment and replacing as necessary.
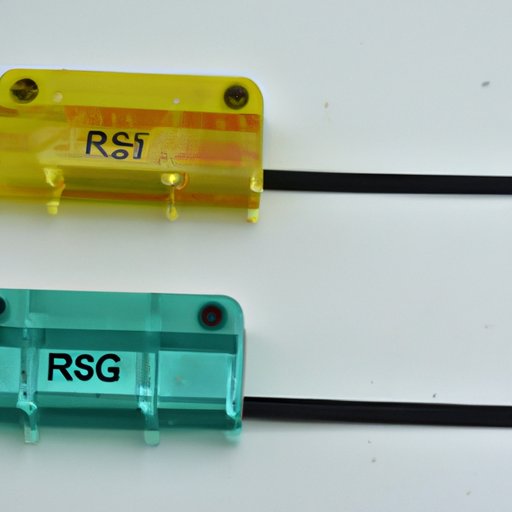
IV. How to Test Automotive Relays
A. Explanation of Common Issues with Automotive Relays
Automotive relays can be prone to failure due to vibration and other environmental factors. Common issues that may arise include:
- Faulty connections: Loose, corroded, or broken connections can cause the relay to stop functioning.
- Coil failure: If the coil is damaged, the relay will not be able to function.
- Worn contacts: Over time, the contacts can wear out or become dirty, leading to a loss of connection.
B. Troubleshooting Steps for Each Issue
To troubleshoot these issues, you can:
- Check connections and clean or replace as necessary.
- Test the coil for continuity or resistance using a multimeter.
- Clean or replace contacts as necessary.
C. Specific Tests and How to Perform Them
To test an automotive relay, you can:
- Check the coil for resistance using a multimeter or a test light. If the coil is not making a connection, replace the relay.
- Check the contacts by using a multimeter or a test light to test for continuity or resistance.
- Verify the switching time by using an oscilloscope to measure the time between the control signal and the switching action.
- Check the contacts for welding or arcing, which can be identified by black or burn marks.
V. Tools Needed to Test a Relay
A. Explanation of the Tools Required to Test a Relay
The tools required to test a relay include:
- A multimeter: Used to measure voltage, current, and resistance.
- An oscilloscope: Used to measure the switching time and waveform of the relay.
- A test light: Used to test for continuity and voltage.
- A heat gun or a hair dryer: Used to test thermal overload relays.
B. How to Properly Use These Tools
To use these tools properly, follow the manufacturer’s instructions and ensure that you are using them in a safe manner. For example, when using a heat gun or a hair dryer, take care not to burn yourself or the relay.
C. Importance of Following Safety Measures When Using Testing Tools
It is essential to follow safety measures when using testing tools and equipment to avoid any potential risks or injuries. Some of these include:
- Wearing personal protective equipment, such as protective eyewear and gloves when necessary.
- Disconnecting all power sources before testing relays.
- Observing safety precautions when working around high voltages and currents.
VI. Common Reasons Why Relays Fail
A. Explanation of Common Causes of Relay Failure
Relay failure can occur due to several reasons, including:
- Excessive heat or vibration
- Electrical overload
- Corrosion or exposure to moisture
- Worn out contacts or coils
B. Preventative Measures That Can Be Taken to Avoid Relay Failure
To prevent relay failure, you can:
- Ensure that relays are correctly installed and secured.
- Perform regular maintenance, including cleaning and inspecting contacts.
- Replace worn-out relays or contacts promptly.
- Use appropriate relays and equipment according to manufacturer recommendations.
C. Tips on How to Identify a Failing Relay
Some signs that a relay may be failing include:
- Circuit failure or erratic operation
- Unusual noises, including buzzing or humming sounds
- Visible signs of damage or wear, such as corrosion or burning
VII. Infographic That Outlines Steps for Testing a Relay
A. Description of the Infographic and Its Purpose
The infographic summarizes the steps involved in testing a relay, providing a visual representation of the process.
B. Visual Representation of the Steps Involved in Testing a Relay
C. Tips and Tricks for Accurate Testing
When testing a relay, it is recommended to:
- Use the appropriate testing tools and equipment for the type of relay being tested.
- Follow manufacturer instructions and safety measures when using testing tools.
- Perform regular testing and maintenance to ensure optimal performance.
VIII. Conclusion
Testing relays is an essential aspect of maintaining electrical systems. Knowing the different relay types, methods to test them, tools required, and potential causes of failure can help prevent equipment damage, personal injury, and other risks. By following these testing methods and taking preventative measures, you can ensure that your relays operate effectively, providing reliable and safe electrical systems.
Remember to follow safety measures, instructions, and seek assistance if you are uncertain about testing methods or equipment.